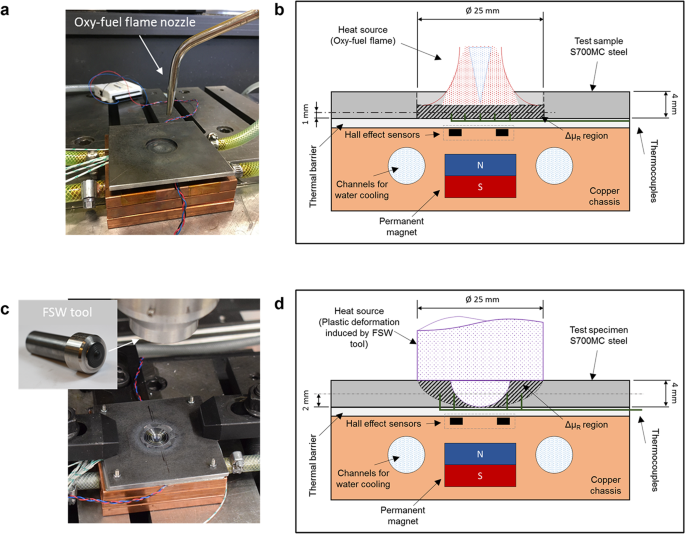
Local magnetic flux density measurements for temperature control of transient and non-homogeneous processing of steels
- Select a language for the TTS:
- UK English Female
- UK English Male
- US English Female
- US English Male
- Australian Female
- Australian Male
- Language selected: (auto detect) - EN
Play all audios:

ABSTRACT Measuring temperatures during high-temperature processing of steels is usually limited to surface measurements that cannot directly assess the internal temperature distribution.
Here, we demonstrate the feasibility of using a magnetic flux density measurement system to assess transient and non-homogeneous temperature fields in a modern high-strength steel, within
the intercritical temperature range where microstructural evolution defines their key mechanical properties. The system accurately detects the Curie temperature and distinguishes temperature
change rates within the processed volume. The magnetic measurements are also sensitive to the volume above Curie temperature and its shape, as revealed when integrated with thermal
computational simulations. The electromagnetic signal provides real-time qualitative and quantitative information relevant to the metallurgical conditions enabling future intelligent control
systems for the production and processing of steels. Contactless measurements of temperature-dependent electromagnetic properties can enable through-thickness temperature monitoring
solutions, opening up opportunities for non-destructive full-field imaging of steels during thermal and thermomechanical processing. SIMILAR CONTENT BEING VIEWED BY OTHERS RESEARCH AND
APPLICATION OF MULTI-FREQUENCY ELECTROMAGNETIC TECHNOLOGY IN REAL-TIME ONLINE CHARACTERIZATION OF STEEL MICROSTRUCTURES AND MECHANICAL PROPERTIES Article Open access 02 January 2025
_IN-OPERANDO_ ANALYSIS OF THE CORROSION PATTERNS AND RATES UNDER MAGNETIC FIELDS USING METALLIC FILM Article Open access 24 March 2022 IN-SITU 3D TEMPERATURE FIELD MODELING AND
CHARACTERIZATION USING EDDY CURRENT FOR METAL ADDITIVE MANUFACTURING PROCESS MONITORING Article Open access 22 March 2025 INTRODUCTION Today, temperature measurements during high-temperature
processing of steels are limited to surface measurements and cannot directly assess the internal temperature distribution. Measurements of the electromagnetic properties are used in
material characterization but mostly in isothermal and homogenous conditions. However, since the electromagnetic properties of steels are temperature-dependent they can be used to develop
new solutions for contactless, non-destructive, temperature monitoring during high-temperature thermal and thermomechanical processing. Steel is the most important engineering material used
worldwide, hence any small increment in quality and energy efficiency during processing is significantly amplified, resulting in global benefits on economic, environmental and social impact.
Nowadays, modern high-strength steels (HSS) offer superior mechanical properties, which enable leaner, lighter and, therefore, more cost-efficient applications. These steels are typically
produced via thermomechanical controlled processing (TMCP)1, a production route that combines controlled rolling and fast cooling to generate the refined microstructure responsible for the
high-strength alongside good toughness2,3,4. Controlling the temperatures during the final TMCP steps is crucial and the role of the intercritical temperature range, between A1 and A3, is
particularly relevant5,6,7,8. Thermal and thermomechanical processing in this temperature domain promotes the microstructure transformation and grain refinement that are responsible for the
enhanced mechanical properties9,10. Frequently, the application of these steels in the fabrication of structures and components requires some form of joining, typically welding. The
sensitivity of the HSS to the high peak temperatures and cooling rates is well established for the widely used fusion welding methods11,12, including the destruction of the original
microstructure and subsequent degradation of strength, toughness and fatigue life13. Solid-state thermomechanical welding processes, such as Friction Stir Welding (FSW), can overcome this
limitation14. FSW of steel can be performed with peak temperatures inside the [A1, A3] range resulting in fine-grained microstructures with mechanical properties that match or even surpass
those of the original base materials15,16,17. Reliable monitoring, both during production of the raw material and in any subsequent thermomechanical processing operation, can support
intelligent control methods that will prevent the severe microstructure degradation occurring above the A3 temperature, and deliver better material properties18,19,20. There are several
methods for measuring temperatures but most are limited to laboratory applications and/or are not suited for high temperature industrial applications21. Typically, in industrial processes,
temperatures are measured using thermocouples and pyrometers22 or infrared cameras13,23. The former are cumbersome since they require contact and only provide point measurements and the
latter are expensive and quite dependent on surface conditions making it difficult to maintain calibration. Furthermore, both are limited to surface temperature measurements and cannot
directly assess the internal temperature, which is critical when a significant in-depth temperature gradient exists or when the heat is generated internally, e.g. via plastic deformation or
oxidation. Thus, there is a need for advanced temperature monitoring solutions, with a fast acquisition rate, enabling high-speed processing and through thickness assessment. The critical
temperatures associated with phase transformations can be identified indirectly with dilatometry measurements24,25. Differential scanning calorimetry (DSC) can also be used with the added
benefit of detecting the ferromagnetic ↔ paramagnetic transformation at the Curie temperature, TC26,27,28. The electromagnetic properties of steel are directly related to microstructure. In
isothermal conditions, electromagnetic measurements are used to study phase fraction29,30,31, hardness32,33,34, stress-states35,36,37, mechanical properties38, and surface
treatments39,40,41. However, the temperature dependence of the electromagnetic properties42,43 can be further exploited to characterize and monitor the steels during transient thermal and
thermomechanical processing44,45,46 with non-homogeneous conditions. We developed a magnetic measurement system that monitors the local magnetic flux density variations, \(\Delta
|\overrightarrow{B}|\), caused by the change of relative magnetic permeability, μR, with varying temperature inside the processed zone. The new measurement system was applied to a S700MC HSS
to assess the thermal condition inside the through-thickness processed volume. Within the optimal processing temperatures for the HSS, [A1, A3], i.e. around TC, the signal is both
qualitatively and quantitatively sensitive to temperature and to temperature change rates. The concept behind this new system was initially conceived for the control of FSW47. The goal was
to combine the benefits of the solid-state thermomechanical FSW process with a real-time monitoring of the full field processing temperatures. Soon it became clear that this concept is
applicable to a wide range of other relevant steel processing methods (with the appropriate sensor architecture development for each specific application). Thus, this scientific
communication is presented in a generalized approach to thermal and thermomechanical processing applications were it is beneficial that the peak temperatures are inside, or in the vicinity,
of the intercritical temperature region. RESULTS EXPERIMENTAL SETUP We developed a magnetic measurement system tailored to identify temperature evolution in the ideal range for
thermomechanical processing of HSS. Figure 1 shows schematic representations of the measurement setup created to monitor the magnetic flux density during thermal and thermomechanical cycles.
The setup consists of a S700MC HSS test specimen clamped to a non-magnetic copper chassis (Fig. 1a) containing the measurement system. Inside the chassis, a permanent magnet generates a
magnetic field, \(\overrightarrow{H}\), that interacts with the steel specimen, changing the magnetic flux density, \(\overrightarrow{B}\), according to the relation
\(\overrightarrow{B}={\mu }_{R}\cdot \overrightarrow{H}\), assuming that magnetic permeability, _μ__R_, is a scalar since the material is considered isotropic. Two (for redundancy)
Hall-effect sensors, positioned between the magnet and the steel, monitor the local magnetic flux density. The location of these sensors was chosen based on the results of the computational
analysis presented in the ‘Computational analysis’ section. Thermocouples positioned at the half-thickness of the processed zones, according to Fig. 1b, measured the temperatures. The
chassis was water cooled to protect the magnet and the magnetic sensors from the effects of the high temperatures. An oxy-fuel flame was used as the heat source for the thermal cycles (Fig.
1c), and plastic deformation induced by a rigid friction stir welding (FSW)48,49 tool was the heat source for the thermomechanical cycles (Fig. 1d). These two heat sources were selected to
decouple the purely thermal effect from any eventual effect of the material flow during the thermomechanical processing that might affect the magnetic measurements. Non-electrical heat
sources were selected to avoid any coercive electromagnetic interaction with the magnetic measurement system. A more detailed description of the experimental setup and procedure is described
in the ‘Methods’ section and in the Supplementary Information file accompanying the online version of this publication. PHASE TRANSFORMATION AND CURIE TEMPERATURES OF S700MC STEEL DSC
measurements with different heating and cooling rates (detailed in the ‘Methods’ section) revealed the presence of three distinct peaks in each cycle. These are labelled 1, 2 and 3 in Fig.
2a. The endothermic peaks inside 1 identify the body centered cubic α iron (e.g. ferrite) → face centred cubic γ iron (austenite) phase transformation between austenite onset temperature,
AC1, and austenite finish temperature, AC3, in the heating stage. The exothermic peaks inside 2 mark the γ → α transformation region between the ferrite onset temperature, AR3, and ferrite
finish temperature, AR1, in the cooling stage. The peaks inside 3 identify TC and their magnitude is smaller than the phase transformation peaks. As with other steels27, the phase change
temperatures depend on the heating/cooling rate but TC is quite stable. A closer analysis of the endothermal reactions during heating at 50 °C/min is presented in Fig. 2b. The peak between
700 and 800 °C corresponds to the ferromagnetic to paramagnetic transformation and its lowest point defines TC = 740 °C. The peak between 800 and 900 °C marks the α ↔ γ phase transformation.
We extrapolated the AC1 and AC3 temperatures by tracing the baseline of the peak and intersecting it with the tangents to the inflection points of the curves. The temperature where the
negative slope tangent intersects the baseline defines AC1 = 826 °C and the temperature where the positive slope tangent intersects the baseline defines AC3 = 882 °C. The austenite to
ferrite transformation onset and finish temperatures on cooling, AR3 and AR1, were determined following the same methodology (Fig. 2c). Since for the 50 °C/min cooling, the TC is inside the
[AR1, AR3] temperature range, the magnetic transformation occurs within the phase transformation and the energetic contributions from these two phenomena are added forming a single
exothermic peak. Considering the relation of the TC with the equilibrium transformation temperatures [A1, A3], an acceptable approximation is [A1, A3] ≈ [AR1, AC3]. COMPUTATIONAL ANALYSIS To
estimate the temperature distribution for the experimental part of this work and to support the design of the magnetic measurement system, we performed computational thermal analyses using
the Finite Element Method (FEM). The analysis established the full temperature fields and identified the volume of material that reaches temperatures above TC, thus, changing from μR≫ 1 to
μR ≈ 1 and becoming paramagnetic, hereafter the paramagnetic volume, Vparamagnetic (Fig. 3). The conditions for the steady-state thermal analysis are described in the ‘Methods’ section.
Superimposing the modelled Vparamagnetic on the etched cross section images of the test specimens reinforces the good agreement between the Vparamagnetic obtained by computational analysis
and the thermomechanically-affected zones (TMAZ) obtained experimentally, further confirming the validity of the model. In a multi-physical approach, we then integrated Vparamagnetic into a
magnetostatic computational analysis to study the interaction of the magnetic field with the test plate upon the ferromagnetic to paramagnetic transformation. The results provide a
visualization of the difference between the magnetic flux density in the presence of a Vparamagnetic in the fully ferromagnetic condition: μR ≫ 1 when T < TC (Fig. 4a,c); _versus_
Vparamagnetic in the paramagnetic condition: μR ≈ 1 when T > TC (Fig. 4b,d). These results were used to support the design of the magnetic measurement system. The optimal position for the
sensors is where the magnetic flux density experiences the greatest variation, comparing the ferromagnetic to paramagnetic states. This occurs mainly inside the paramagnetic volume itself
and in its immediate vicinity. Since the inside of the material is inaccessible and the heat sources occupy the space above the Vparamagnetic, the magnetic sensors were positioned below
Vparamagnetic. EXPERIMENTAL MEASUREMENTS OF TEMPERATURE AND MAGNETIC PERMEABILITY DURING THERMAL AND THERMOMECHANICAL CYCLES The magnetic measurement system, introduced in the ‘Experimental
setup’ section, was used to monitor the magnetic flux density and the temperature during the thermal and thermomechanical cycles (see details in ‘Methods’ section). The different cycles are
identified according to heat source - Flame or FSW tool - and maximum temperature above _or_ below the Curie temperature: TMAX > TC _or_ TMAX < TC. In Figs. 5 and 6, the plotted
temperature curves correspond to the thermocouple that registered the highest temperature in each measurement (i.e. the one closest to the heat source). The magnetic measurements are
represented as magnetic flux density variation, \(\Delta |\overrightarrow{B}|\), from a baseline defined as the initial value of \(|\overrightarrow{B}|\). Positive values of \(\Delta
|\overrightarrow{B}|\) indicate increases of μR in the processed material whereas the opposite applies for negative values of \(\Delta |\overrightarrow{B}|\). The results for the Flame_TMAX
< TC cycle are presented in Fig. 5a. The maximum temperature does not go over TC and there is no drop in magnetic flux density, indicating that TC was not reached anywhere in the
specimen. Similarly, in the FSW_TMAX < TC cycle (Fig. 5b) the maximum temperature measured did not exceed TC and no drop in Δ\(|\overrightarrow{B}|\) occurs. It is worth mentioning that
even though the whole processed volume of the steel specimens is kept below the Curie temperature the Δ\(|\overrightarrow{B}|\) moves slightly away from the baseline. This phenomena of
sensitivity of the magnetic measurement to different temperatures below the TC is reported by other authors50,51,52. The Flame_TMAX > TC measurements are shown in Fig. 6a. TMAX surpassed
TC and, accordingly, the magnetic flux sensors detected a clear decrease in signal strength, followed by a return to the baseline when the temperature dropped below TC at the end of the
cycle. The magnetic sensors registered the signal decrease about Δt1 = 12.8 seconds before the thermocouple recorded values above TC. This offset is due to the fact that the thermocouple
provides a point measurement while the magnetic measurement is immediately sensitive to the change in μR, caused by temperatures above TC, anywhere in the volume of processed material,
starting from the vicinity of the power source. This delay is opposite during the cooling, for the same reason. Note that Δt2 < Δt1 which reflects the difference in temperature change
rate between heating and cooling periods. The FSW_TMAX > TC measurements, presented in Fig. 6b, exhibit all the same characteristics as those described for Flame_TMAX > TC, and contain
additional distinguishable features of the notable significance. The distinguishable effect, depicted in Fig. 6b, is an inverse systematic relation between the \(\Delta
|\overrightarrow{B}|\) rate and the heating rate. During the dwell phase of the thermomechanical cycle, the temperature curve exhibits two different heating rates, represented by blue dotted
lines marked \(\frac{\Delta {T}_{1}}{\Delta {t}_{1}}=3.4\) and \(\frac{\Delta {T}_{2}}{\Delta {t}_{2}}=0.2\) °C/s. The two heating rates are reflected in the \(\Delta |\overrightarrow{B}|\)
_versus_ time graph as indicated by blue dotted lines marked \(\frac{\Delta {|\overrightarrow{B}|}_{1}}{\Delta {t}_{1}}=-\,1.1\) and \(\frac{\Delta {|\overrightarrow{B}|}_{2}}{\Delta
{t}_{2}}=-\,0.7\) Gauss/s. This means that the measurement system not only accurately detects the TC, but is also sensitive to the effect of temperature change rates within the processed
volume. This quantitative effect is of the upmost importance because it has not been found in the existing literature and it opens up the possibility of implementing new intelligent control
systems. As an example, the Δ\(|\overrightarrow{B}|\) signal can be used as an input for a control system to maintain the temperatures during steel production or processing inside the
[≈A1,TC] range. The results of a more detailed investigation of the sensitivity of the \(\Delta |\overrightarrow{B}|\) to the volume above Curie temperature, Vparamagnetic, will be presented
next. MAGNETIC FLUX DENSITY MEASUREMENTS VERSUS MATERIAL VOLUME ABOVE CURIE TEMPERATURE We estimated Vparamagnetic, i.e. the volume of material with T > TC, at five different instants
during the heating phase of Flame_TMAX > TC and FSW_TMAX > TC via computational analysis. Figure 7 shows the relationship between Vparamagnetic and the change in magnetic flux density
\(\varDelta |\overrightarrow{B}|\) relative to the initial value \({|\overrightarrow{B}|}_{{t}_{0}}\). Visual representations of the different volumes are included to support the
interpretation of results. Power law curves, _f_(_x_) = _kx__n_, where \(x={V}_{paramagnetic}\) and \(f(x)=\frac{\Delta |\overrightarrow{B}|}{{|\overrightarrow{B}|}_{{t}_{0}}}\), were fitted
to the thermal cycle data (\(k=0.03993\); \(n=0.282\)) and to the thermomechanical cycle data (\(k=0.003636\); \(n=0.574\)). The two curves show that though ΔVparamagnetic is smaller in the
thermal cycle (Flame) than in the thermomechanical cycle (FSW tool) it has a stronger effect on \(\frac{\varDelta |\overrightarrow{B}|}{{|\overrightarrow{B}|}_{{t}_{0}}}\). Observing the
visual representations of the paramagnetic volumes we can identify two different stages in the evolution of \({V}_{paramagneti{c}_{}}\). The first stage is dominated by an increase in the
thickness of \({V}_{paramagneti{c}_{}}\) (i.e. \(\varDelta V\propto \varDelta t\), where t is the thickness) and is more pronounced in \({{\rm{V}}}_{paramagneti{c}_{(Flame)}}\). The second
stage is dominated by radial expansion (i.e. \(\varDelta V\propto \varDelta d\), where _d_ is the diameter) and is more evident in the evolution of
\({{\rm{V}}}_{paramagneti{c}_{(FSWtool)}}\). These results suggest that \(\frac{\varDelta |\overrightarrow{B}|}{{|\overrightarrow{B}|}_{{t}_{0}}}\) is sensitive to the shape of the
paramagnetic volumes and to the way those shapes evolve over time. DISCUSSION The peak temperatures and the temperature change rates control the grain size evolution, precipitation and
solution, which along with the strain hardening are responsible for the microstructure of steels and their mechanical properties. These phenomena depend mostly on the thermal and
thermomechanical history across the intercritical temperature domain12, where the Curie temperature lies and the α ↔ γ phase transformation of iron structures occurs. We developed a
non-destructive, contactless, magnetic-based measurement system that exploits the temperature dependence of the electromagnetic properties to assess temperature domains inside a volume of
processed steel. By monitoring the change of magnetic flux density near the Curie temperature, our system provides real-time qualitative and quantitative information related to the
temperature field within the intercritical temperature domain. This enables the development of intelligent systems capable of assessing and controlling the phenomena that govern the
metallurgical and mechanical properties of steels, which is of special relevance in the thermal and thermomechanical processing of modern high-strength steels. Examples of processes
associated with an external heat source resulting in thermal processing, approximated in the paper by the thermal cycles using the flame as external the heat source, are i) with fusion:
oxi-fuel welding and cutting, laser welding and cutting, electron beam welding, electric arc based welding and cutting; ii) without fusion: heat treatment, e.g. plasma, flame, high-frequency
induction (where the sensor can be integrated with the induction coil). Examples of processes associated with thermomechanical processing, where the heat source is internal, i.e. the
material, by energy dissipation during its bulk plastic deformation, are the FSW (partially addressed in the paper by the thermomechanical cycles using the plunge and dwell stages of a FSW
tool), the friction welding, forging, hot rolling during steel production. The multiphysical research plan encompassed DSC experimental measurements, computational thermal analysis and
dedicated design and implementation of the magnetic-based measurement system. The DSC measurements with different heating and cooling rates were used to establish, with precision and
reliability, the Curie temperature, TC ≈ 740 °C, and the transformation temperatures, [AR1, AC3] = [702 °C, 882 °C], of the S700MC high-strength steel used as test specimen. The
transformation temperatures considered were the ones obtained with the 50 °C/min rate as they are the ones closer to real processing conditions. The Curie temperature showed no dependence on
the heating or cooling rates. The computational thermal analysis was used to support the design of the magnetic measurement system and identify the volume of material that reaches
temperatures above TC, thus, changing from μR ≫ 1 to μR ≈ 1 and becoming paramagnetic. The results show that our magnetic flux density measurements can be used to detect the magnetic
transformation of the processed volume when it reaches the Curie temperature. Above this temperature, it is also sensitive to the effect of temperature change rates within the processed
volume. Additionally, based on the multiphysical approach, the measurements provide sensitive data related to the evolution of the processed volume, namely, it can discern between different
heating and cooling rates and between the effects of different changes in shape (Δ thickness vs Δ diameter). There is a \(\varDelta |\overrightarrow{B}|\) associated with a small magnetic
permeability increase below the Curie temperature indicating that the temperatures inside processed volume are changing, this may also represent a valuable information for a control system
and should be studied in more detail. The new and distinguishable results presented in this work result from two major differences in the implemented research plan when compared with the
state of the art in this field, namely: (i) the measurements of the magnetic properties are performed during transient thermal processing with complex non-homogenous conditions; (ii) besides
an external purely heat power source (i.e. a flame), the work included thermomechanical processing. In this case, the specimen materials become the heat power source, due to the heat
generated by internal viscous energy dissipation during the non-homogeneous plastic deformation of the material and superficial frictional energy dissipation in the contact with the rigid
FSW tool. The internal energy dissipation decreases as the temperature increases and, so, the thermomechanical processing resulted in steady-state heating rates, different for different
stages of the deformation. This yielded the opportunity for the magnetic measurement system to show unique capabilities, besides accurately detecting the TC, such as being sensitive to the
effect of temperature change rates within the processed volume. For full temperature range measurements other complementary measurement methods, such as pyrometers and infrared thermography
systems, can be integrated via data fusion processes. This through-thickness, contactless, monitoring solution (that can provide real-time data on the temperatures and temperature rates
inside a volume of material under non-uniform and transient conditions) will contribute to bring steel production and processing in line with the new digitalization paradigm by providing
large amounts of information rich data that can be readily available to support highly integrated, smart, cyber-physical manufacturing systems53. Going digital in the fabrication of
steel-based structural systems and products, will allow zero-defect factories with safer working conditions and lower environmental impact. The next steps will be to expand the capabilities
of the measurement system from a single Hall-effect sensor configuration to multiple sensors forming an array. This will provide data with spatial resolution and enable image reconstruction
of the processed volume of material. With a dedicated multiphysical solution, integrating computational simulation of the metallurgical evolution and thermal analysis with the
non-destructive real-time magnetic measurement system presented here, it will be possible to deliver a full field imaging solution for application in intelligent automated control systems
for steel production and processing. METHODS MATERIAL The base material used in this study was a S700MC high-strength steel produced by TMCP, whose chemical composition is: [max. wt.%] 0.059
C; 0.205 SI; 1.79 Mn; 0.007 P; 0.002 S; 0.026 Al; 0.083 Nb; V; 0.013; 0.113 T. The specimens used in the thermal and thermomechanical processing cycles were 100 × 100 × 4 mm plates. For the
thermal cycles (oxy-fuel flame heat source), a region of reduced thickness (2 mm) was produced on the middle of the plates, by removing Ø 25 × 2 mm of material by machining as depicted in
Fig. 1c, to concentrate the heating effect. Similarly, for the thermomechanical cycles (FSW tool heat source) a Ø 10 mm and 3.5 mm deep hole (Fig. 1d) was drilled at the center of the plates
to remove a volume of material roughly equivalent to that of the tool probe. DIFFERENTIAL SCANNING CALORIMETRY (DSC) Differential scanning calorimetry measurements were performed on a
NETZSCH STA 449F1 equipment, capable of a maximum heating rate of 50 °C/s. A sample of the S700MC steel (approximately 1.5 × 2 × 3 mm and 75 mg) was placed inside an Al2O3 ladle and the
measurements were carried out under a protective Argon atmosphere. The thermal cycles comprised four stages: 1 - holding at 100 °C; 2 – heating (at 50, 20, 10, and 5 °C/min); 3 - holding at
1000 °C; and 4 – cooling (at 50, 20, 10, and 5 °C/min). The cycles were carried out three times per heating/cooling rate. The holding times were 5 min. COMPUTATIONAL ANALYSES Transient
thermal computational analyses were performed using the commercial ANSYS Workbench 19.0 software. The purpose of these analyses was to obtain the temperature fields in agreement with the
temperature measurements obtained experimentally via thermocouples and to estimate the volume of material that reached temperatures above TC. The geometries used were the same as shown in
Fig. 1a and 1c, with the specific sample geometry for each heat source (i.e. a region of reduced thickness in the case of the flame as heat source, and the negative of the FSW tool in the
case of the FSW tool as the heat source). The meshes were comprised of about 3.8 million (flame as heat source case) and 3 million (FSW tool as heat source case) tetrahedron elements. The
maximum element size was 0.5 mm in the steel plates and 1 mm in all other bodies. The loading condition representing the flame was a heat flow with a normal distribution applied on the
surface of the reduced thickness region of the steel specimen body. The analysis was carried out in one step. The loading conditions representing the effect of the heat flow from the FSW
tool were applied on the surfaces corresponding to the negative of the tool geometry. The analysis was carried out in two steps. The first step with heat flow applied only on the surfaces
corresponding to the probe, and the second step adding the heat flow contribution on the surfaces corresponding to the shoulder. The final results were obtained by adjusting loading
conditions iteratively until the simulated temperature fields were in close agreement with the thermocouple measurements for each case. In both cases, the initial temperature was 25 °C, and
a constant temperature of 25 °C was applied to the surfaces corresponding to the inside of the copper cooling tubes. An emissivity of 0.3 was considered at the top surface of the steel
specimen, excluding the heat flow loading surfaces. All other outside surfaces were adiabatic. The material models used were those for Steel 1010, Copper, Titanium, and Air, available in the
materials library of the ANSYS Workbench 19.0 software. The results were validated by comparing the temperature fields above the TC, obtained computationally, with the heat-affected zones
evaluated in cross-sections of samples extracted from the center of the processed specimens. A table with the material thermal properties, figures and graphs supporting the methods
implemented in the thermal analyses are included in the “Suplementary Information” file available with the online version of this paper. The magnetostatic computational analyses were
performed using the ANSYS Maxwell R18.0 software. The geometries were the same as in the thermal analyses. The meshes were comprised of 2.8 million tetrahedron elements (in both the flame
and the FSW tool analyses). The volumes obtained from the thermal analysis were integrated into the magnetostatic model and the analyses were carried out for different values of magnetic
permeability (μR ≫ 1 vs μR ≈ 1) in those volumes. The material models used were those for Steel 1010, Copper, Titanium, Air and NdFe35, available in the materials library of the ANSYS
Maxwell R18.0 software. A table with the magnetic properties considered for the materials is included in the “Suplementary Information” file available with the online version of this paper.
THERMAL AND THERMOMECHANICAL CYCLES WITH TEMPERATURE AND MAGNETIC FLUX DENSITY MEASUREMENTS Thermal and thermomechanical cycles were carried out on S700MC HSS using non-electrical heat
sources to avoid any coercive electromagnetic interaction with the magnetic measurement system. Two heat sources were applied to the specimens: For the thermal cycles it was an oxy-fuel
flame, which is a purely thermal heat source; and for the thermomechanical cycles it was the thermomechanical processing, which is an indirect heat source via internal friction dissipation
during the plastic deformation induced in the HSS specimen by the plunging and rotation of a rigid FSW tool. The tool material was a non-magnetic polycrystalline cubic boron nitride in a
tungsten rhenium metal matrix. Thermocouples were inserted into small holes reaching the half thickness of the processed zone of the specimens. A spacing of 5 mm was kept between each
thermocouple as shown in Supplementary Figure S2 in the Supplementary Information file. The ‘Experimental setup’ section described the main features of test setup, depicted in Fig. 1. The
magnet used to generate the magnetic field was a Ø 15 × 8 mm NeFeB permanent magnet with N42 magnetization in the axial direction. The distance from the magnet to the test sample was such
that the interaction between the field and the sample generates the largest field intensity variation when the material changes from ferromagnetic to paramagnetic (and vice versa) without
saturating the signal from the Hall-effect sensors. A good compromise between these two conditions was achieved at a distance of 13 mm, directly under the processed zone. The two sensors
used to measure the magnetic flux density were SS496A1 ratiometric Hall-effect sensors. These were positioned in 2 mm deep slots machined on the copper chassis at ±5 mm from the center of
the plate. The positioning of these sensors, relative to the permanent magnet and the test plate, was supported by the results of the magnetostatic computational analysis. The chassis was
water cooled to protect the magnet and the magnetic sensors from the effects of the high temperatures. Furthermore, a 3 mm thick thermal barrier (air gap for the thermal cycles and a Ti
plate for the thermomechanical cycles) was placed between the copper chassis and the steel test piece for additional protection of the magnet and the sensors from the high temperature, and
also to provide additional backing support in the case of thermomechanical cycles. The data from the Hall-effect sensors and the thermocouples was acquired via a NI USB-6008 module and a
NI-9212 module, respectively. A custom-made application was created in LabVIEW to control and synchronize the data acquisition and recording. The data acquisition rate used was 10 Samples/s
(10 Hz) which was sufficient to capture with high resolution all the magnetic flux density gradients in the tested thermal and thermomechanical transient processes. DATA AVAILABILITY
Supplementary information is available in the document accompanying the online version of this publication. REFERENCES * Zhao, J. & Jiang, Z. Thermomechanical processing of advanced high
strength steels. _Prog. Mater. Sci._ 94, 174–242 (2018). Article CAS Google Scholar * Zhao, M. C., Yang, K. & Shan, Y. The effects of thermo-mechanical control process on
microstructures and mechanical properties of a commercial pipeline steel. _Mater. Sci. Eng. A_ 335, 14–20 (2002). Article Google Scholar * Xue, X. H., Shan, Y. Y., Zheng, L. & Lou, S.
N. Microstructural characteristic of low carbon microalloyed steels produced by thermo-mechanical controlled process. _Mater. Sci. Eng. A_ 438–440, 285–287 (2006). Article CAS Google
Scholar * Endo, S. & Nakata, N. Development of Thermo-Mechanical Control Process (TMCP) and high performance steel in JFE Steel. _JFE Tech. Rep._ 20, 1–7 (2015). Google Scholar *
Movahed, P., Kolahgar, S., Marashi, S. P. H., Pouranvari, M. & Parvin, N. The effect of intercritical heat treatment temperature on the tensile properties and work hardening behavior of
ferrite-martensite dual phase steel sheets. _Mater. Sci. Eng. A_ 518, 1–6 (2009). Article CAS Google Scholar * Shi, L. _et al_. Improved toughness and ductility in ferrite/acicular
ferrite dual-phase steel through intercritical heat treatment. _Mater. Sci. Eng. A_ 590, 7–15 (2014). Article CAS Google Scholar * Shukla, R., Ghosh, S. K., Chakrabarti, D. &
Chatterjee, S. Microstructure, texture, property relationship in thermo-mechanically processed ultra-low carbon microalloyed steel for pipeline application. _Mater. Sci. Eng. A_ 587, 201–208
(2013). Article CAS Google Scholar * Cao, W. _et al_. Ultrahigh Charpy impact toughness (<450J) achieved in high strength ferrite/martensite laminated steels. _Sci. Rep._ 7, 1–8
(2017). Article CAS Google Scholar * Humphreys, F. J., Prangnell, P. B. & Priestner, R. Fine-grained alloys by thermomechanical processing. _Curr. Opin. Solid State Mater. Sci._ 5,
15–21 (2001). Article ADS CAS Google Scholar * Arora, H. S. _et al_. High Tensile Ductility and Strength in Dual-phase Bimodal Steel through Stationary Friction Stir Processing. _Sci.
Rep._ 9, 1–6 (2019). Article ADS CAS Google Scholar * Kim, B. C., Lee, S., Kim, N. J. & Lee, D. Y. Microstructure and local brittle zone phenomena in high-strength low-alloy steel
welds. _Metall. Trans. A_ 22, 139–149 (1991). Article Google Scholar * Górka, J. Assessment of Steel Subjected to the Thermomechanical Control Process with Respect to Weldability. _Metals
(Basel)._ 8, (169 (2018). Google Scholar * Górka, J., Janicki, D., Fidali, M. & Jamrozik, W. Thermographic Assessment of the HAZ Properties and Structure of Thermomechanically Treated
Steel. _Int. J. Thermophys._ 38, 1–21 (2017). Article CAS Google Scholar * Thomas, W. M., Threadgill, P. L. & Nicholas, E. D. Feasibility of friction stir welding steel. _Sci.
Technol. Weld. Join._ 4, 365–372 (1999). Article CAS Google Scholar * Lienert, T. & Jr, W. S. Friction stir welding studies on mild steel. _Weld. J. Res. Suppl._ 82, 1–9 (2003).
Google Scholar * Morisada, Y. _et al_. Improvement of toughness and strength of thick structural steel weld by friction stir welding conditions. _Sci. Technol. Weld. Join._ 18, 287–292
(2013). Article CAS Google Scholar * Xue, P., Komizo, Y., Ueji, R. & Fujii, H. Enhanced mechanical properties in friction stir welded low alloy steel joints via structure refining.
_Mater. Sci. Eng. A_ 606, 322–329 (2014). Article CAS Google Scholar * Fujii, H. _et al_. Friction stir welding of carbon steels. _Mater. Sci. Eng. A_ 429, 50–57 (2006). Article CAS
Google Scholar * Sorger, G. _et al_. Microstructure and fatigue properties of friction stir welded high-strength steel plates. _Sci. Technol. Weld. Join._ 1718, 1–7,
https://doi.org/10.1080/13621718.2017.1399574 (2017). Article CAS Google Scholar * Sorger, G., Sarikka, T. & Vilaça, P. Effect of processing temperatures on the properties of a
high-strength steel welded by FSW. _Weld. World_, https://doi.org/10.1007/s40194-018-0612-8 (2018). Article CAS Google Scholar * Childs, P. R. N., Greenwood, J. R. & Long, C. A.
Review of temperature measurement. _Rev. Sci. Instrum._ 71, 2959–2978 (2000). Article ADS CAS Google Scholar * Müller, B., Renz, U., Hoppe, S. & Klocke, F. Radiation Thermometry at a
High-Speed Turning Process. _J. Manuf. Sci. Eng._ 126, 488 (2004). Article Google Scholar * Davies, M. A., Ueda, T., M’Saoubi, R., Mullany, B. & Cooke, A. L. On The Measurement of
Temperature in Material Removal Processes. _CIRP Ann. - Manuf. Technol._ 56, 581–604 (2007). Article Google Scholar * Kop, T. A., Sietsma, J. & Van Der Zwaag, S. Dilatometric analysis
of phase transformations in hypo-eutectoid steels. _J. Mater. Sci._ 36, 519–526 (2001). Article ADS CAS Google Scholar * García De Andrés, C., Caballero, F. G., Capdevila, C. &
Álvarez, L. F. Application of dilatometric analysis to the study of solid-solid phase transformations in steels. _Mater. Charact._ 48, 101–111 (2002). Article Google Scholar * Kargul, T.
Investigations of Temperatures of Phase Transformations of Low-Alloyed Reinforcing Steel within the Heat Treatment Temperature Range. _Arch. Metall. Mater._ 62, 891–897 (2017). Article CAS
Google Scholar * Raju, S., Ganesh, B. J., Banerjee, A. & Mohandas, E. Characterisation of thermal stability and phase transformation energetics in tempered 9Cr-1Mo steel using drop
and differential scanning calorimetry. _Mater. Sci. Eng. A_ 465, 29–37 (2007). Article CAS Google Scholar * Jeya Ganesh, B. _et al_. Differential scanning calorimetry study of diffusional
and martensitic phase transformations in some 9 wt-%Cr low carbon ferritic steels. _Mater. Sci. Technol._ 27, 500–512 (2010). Article CAS Google Scholar * Ghanei, S., Kashefi, M. &
Mazinani, M. Eddy current nondestructive evaluation of dual phase steel. _Mater. Des._ 50, 491–496 (2013). Article CAS Google Scholar * Zhou, L. _et al_. Quantification of the phase
fraction in steel using an electromagnetic sensor. _NDT E Int._ 67, 31–35 (2014). Article CAS Google Scholar * Yin, W., Peyton, A. J., Strangwood, M. & Davis, C. L. Exploring the
relationship between ferrite fraction and morphology and the electromagnetic properties of steel. _J. Mater. Sci._ 42, 6854–6861 (2007). Article ADS CAS Google Scholar * Sorger, G. L.
_et al_. Non-destructive microstructural analysis by electrical conductivity: comparison with hardness measurements in different materials. _J. Mater. Sci. Technol_,
https://doi.org/10.1016/j.jmst.2018.09.047 (2018). Article Google Scholar * Xu, H. _et al_. Imaging x70 weld cross-section using electromagnetic testing. _NDT E Int._ 98, 155–160 (2018).
Article CAS Google Scholar * Yu, C. _et al_. Measurement of the Hardness of Medium Carbon Steel Using the Magnetic Mixing-Frequency Technique. _IEEE Trans. Magn_. 54 (2018). Article
Google Scholar * Makar, J. & Tanner, B. The _in situ_ measurement of the effect of plastic deformation on the magnetic properties of steel. _J. Magn. Magn. Mater._ 184, 193–208 (2002).
Article ADS Google Scholar * Perevertov, O. Influence of the applied elastic tensile and compressive stress on the hysteresis curves of Fe-3%Si non-oriented steel. _J. Magn. Magn. Mater._
428, 223–228 (2017). Article ADS CAS Google Scholar * Qiu, F., Ren, W., Tian, G. Y. & Gao, B. Characterization of applied tensile stress using domain wall dynamic behavior of
grain-oriented electrical steel. _J. Magn. Magn. Mater._ 432, 250–259 (2017). Article ADS CAS Google Scholar * Aghadavoudi-Jolfaei, M., Shen, J., Smith, A., Zhou, L. & Davis, C. L.
Non-destructive measurement of microstructure and tensile strength in varying thickness commercial DP steel strip using an EM sensor. _J. Magn. Magn. Mater._ 473, 477–483 (2019). Article
ADS CAS Google Scholar * Perevertov, O., Stupakov, O., Tomáš, I. & Skrbek, B. Detection of spring steel surface decarburization by magnetic hysteresis measurements. _NDT E Int._ 44,
490–494 (2011). Article CAS Google Scholar * Zhu, W. _et al_. Evaluation of rail decarburisation depth using a H-shaped electromagnetic sensor. _NDT E Int._ 46, 63–69 (2012). Article CAS
Google Scholar * Liu, J. _et al_. Electromagnetic evaluation of the microstructure of Grade 91 tubes/pipes. _Int_. _J. Press. Vessel. Pip._ 132–133, 65–71 (2015). Article CAS Google
Scholar * Cedillo, E., Ocampo, J., Rivera, V. & Valenzuela, R. An apparatus for the measurement of initial magnetic permeability as a function of temperature. _J. Phys. E._ 13, 383–386
(1980). Article ADS CAS Google Scholar * Morishita, M., Takahashi, N., Miyagi, D. & Nakano, M. Examination of magnetic properties of several magnetic materials at high temperature.
_Prz. Elektrotechniczny (Electrical Rev._ 87,, 106–110 (2011). Google Scholar * Yamamura, H., Toh, T., Harada, H., Takeuchi, E. & Ishii, T. Optimum magnetic flux density in quality
control of casts with level DC magnetic field in continuous casting mold. _ISIJ Int._ 41, 1229–1235 (2001). Article CAS Google Scholar * Kuz’ko, E. I., Belomyttsev, M. Y. & Belov, V.
A. A Study of Phase Transformations in High-Chromium Ferritic-Martensitic Steels by Magnetometry. _Met. Sci. Heat Treat._ 60, 259–265 (2018). Article ADS CAS Google Scholar * Harada, H.,
Nagashima, M., Konno, T., Yamana, M. & Toh, T. Electromagnetic sensor just below CC mold by using magnetic transformation of steel. _IOP Conf. Ser. Mater. Sci. Eng_. 424 (2018). *
Sorger, G., Vilaça, P. & Santos, T. G. Concept and Architecture of a New Advanced Control for the FSW of Steels. _Proc. 11th Int. Symp. Frict. Stir Weld_. (2016). * Vilaça, P. &
Thomas, W. In _Structural Connections for Lightweight Metallic Structures_ (eds. Moreira, P. M. G. P., da Silva, L. F. M. & de Castro, P. M. S. T.) 85–124,
https://doi.org/10.1007/8611_2011_56 (Springer Berlin Heidelberg, 2012). Chapter Google Scholar * Mishra, R. S. & Ma, Z. Y. Friction stir welding and processing. _Mater. Sci. Eng. R
Reports_ 50, 1–78 (2005). Article CAS Google Scholar * Zhou, L., Hall, R. & Davis, C. L. Measured and modelled low field relative permeability for dual phase steels at high
temperature. _J. Magn. Magn. Mater._ 475, 38–43 (2019). Article ADS CAS Google Scholar * Boehm, A. & Hahn, I. Measurement of magnetic properties of steel at high temperatures. _Ind.
Electron. Soc. IECON 2014-40th Annu. Conf. IEEE_ 715–721 (2014). * Takahashi, N., Morishita, M., Miyagi, D. & Nakano, M. Examination of magnetic properties of magnetic materials at high
temperature using a ring specimen. _IEEE Trans. Magn._ 47, 4352–4355 (2011). Article ADS CAS Google Scholar * Monostori, L. _et al_. Cyber-physical systems in manufacturing. _CIRP Ann._
65, 621–641 (2016). Article Google Scholar Download references ACKNOWLEDGEMENTS Gonçalo Sorger thankfully acknowledges the financial support provided by the School of Engineering of Aalto
University. Telmo G. Santos acknowledges FCTMCTES for its financial support via the project UID/EMS/00667/2019 (UNIDEMI). AUTHOR INFORMATION AUTHORS AND AFFILIATIONS * Department of
Mechanical Engineering, School of Engineering, Aalto University, 02150, Espoo, Finland Gonçalo Sorger & Pedro Vilaça * UNIDEMI, Department of Mechanical and Industrial Engineering, NOVA
School of Science and Technology, Universidade NOVA de Lisboa, 2829-516, Caparica, Portugal Telmo G. Santos Authors * Gonçalo Sorger View author publications You can also search for this
author inPubMed Google Scholar * Pedro Vilaça View author publications You can also search for this author inPubMed Google Scholar * Telmo G. Santos View author publications You can also
search for this author inPubMed Google Scholar CONTRIBUTIONS G.S., T.G.S. and P.V. contributed to the discussion on the concept, design and applications of the magnetic-based measurement
system. G.S. constructed the measurement system, developed the LabVIEW data acquisition software and carried out all of the experiments. G.S. and P.V. contributed to the computational
thermal analysis. G.S. and T.G.S. contributed to the magnetostatic computational analysis. G.S. and P.V. contributed to the analysis and discussion of results. G.S. and P.V. contributed to
writing the paper. All authors reviewed the manuscript. CORRESPONDING AUTHOR Correspondence to Gonçalo Sorger. ETHICS DECLARATIONS COMPETING INTERESTS The authors declare no competing
interests. ADDITIONAL INFORMATION PUBLISHER’S NOTE Springer Nature remains neutral with regard to jurisdictional claims in published maps and institutional affiliations. SUPPLEMENTARY
INFORMATION SUPPLEMENTARY INFORMATION RIGHTS AND PERMISSIONS OPEN ACCESS This article is licensed under a Creative Commons Attribution 4.0 International License, which permits use, sharing,
adaptation, distribution and reproduction in any medium or format, as long as you give appropriate credit to the original author(s) and the source, provide a link to the Creative Commons
license, and indicate if changes were made. The images or other third party material in this article are included in the article’s Creative Commons license, unless indicated otherwise in a
credit line to the material. If material is not included in the article’s Creative Commons license and your intended use is not permitted by statutory regulation or exceeds the permitted
use, you will need to obtain permission directly from the copyright holder. To view a copy of this license, visit http://creativecommons.org/licenses/by/4.0/. Reprints and permissions ABOUT
THIS ARTICLE CITE THIS ARTICLE Sorger, G., Vilaça, P. & Santos, T.G. Local magnetic flux density measurements for temperature control of transient and non-homogeneous processing of
steels. _Sci Rep_ 9, 17900 (2019). https://doi.org/10.1038/s41598-019-54503-5 Download citation * Received: 28 June 2019 * Accepted: 14 November 2019 * Published: 29 November 2019 * DOI:
https://doi.org/10.1038/s41598-019-54503-5 SHARE THIS ARTICLE Anyone you share the following link with will be able to read this content: Get shareable link Sorry, a shareable link is not
currently available for this article. Copy to clipboard Provided by the Springer Nature SharedIt content-sharing initiative